First Class Design for Protection of the Environment
MINING and METALS SULPHUR TECHNOLOGIES
Rameshni & Associates Technology & Engineering (RATE) has the unrivalled ability to address all sulphur removal and handling issues across all industry sectors including Mining and Metals, and Smelters. RATE has recently patented three new processes for Reduction of SO2 to Sulphur. Sulphur dioxide is found in many industrial gases emanating from plants involved in roasting, smelting and sintering sulfide ores, or gases from power plants burning high sulphur coal or fuel oils or other sulphurous ores or other industrial operations involved in the combustion of sulphur-bearing fuels, such as fuel oil. One of the more difficult environmental problems facing industry is how to economically control SO2 emissions from these sources. Production of sulphur is an alternate solution to sulphuric acid where dealing with remote location and limited transportation of sulphuric acid as well as limited market demand for sulphuric acid.
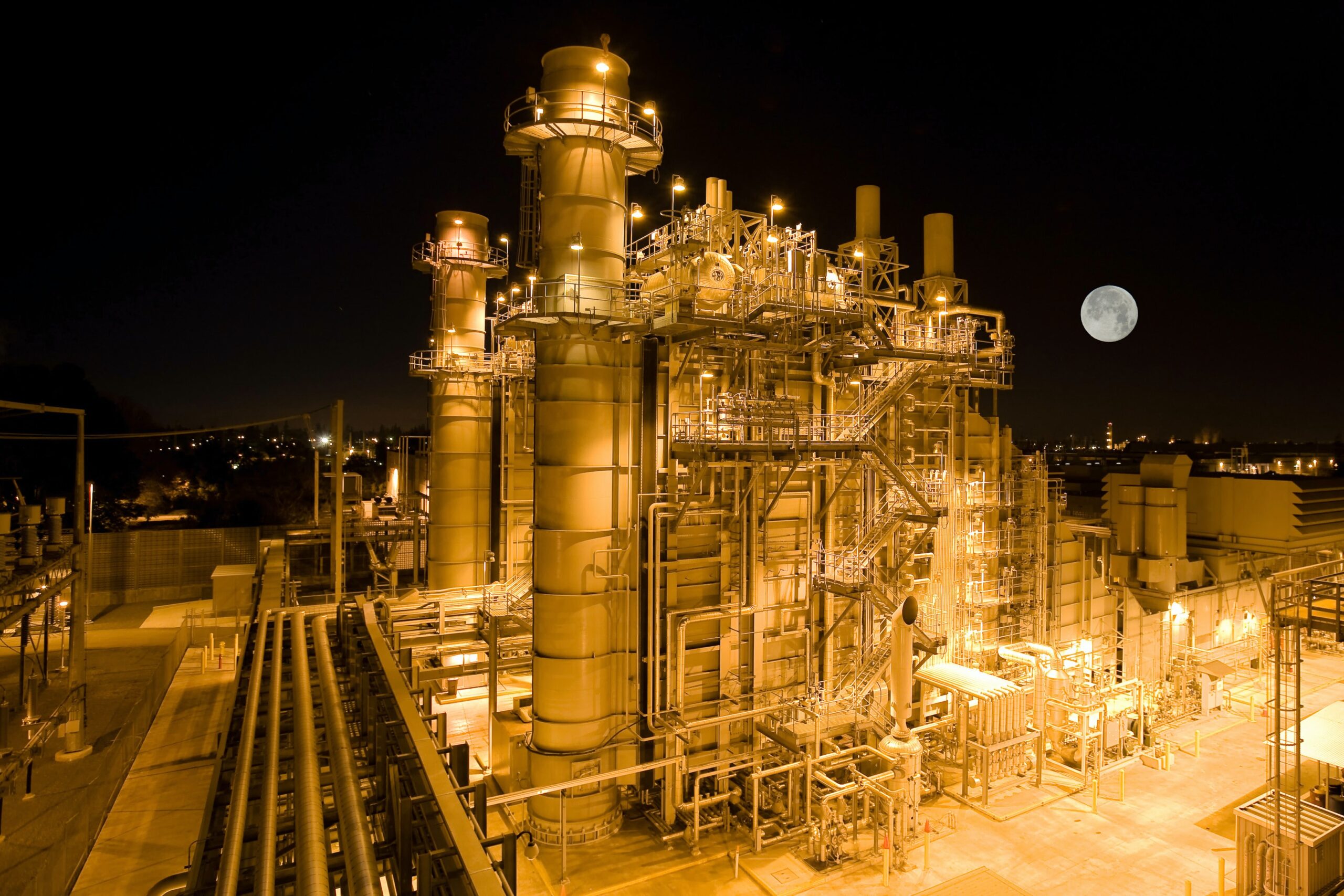
The new innovations have superior advantages to other existing processes with the overall sulphur recovery near 100%. A summary of each patent is described below.
Process for the Production of Sulphur from Sulphur Dioxide with Tail Gas
Recycle – The present invention relates to a process for recovering Sulphur from Sulphur dioxide (SO2) containing gases. Key advantages are lower fuel consumption, reduced emissions, better product Sulphur quality, better operational stability and increased safety without producing by products such as CS2 with the Sulphur recovery of above 97% and overall recovery of 100%.
Thermal Reduction of Sulphur Dioxide to Sulphur with Temperature
Controlled Furnace
Recycle – The present invention relates to a process for recovering
sulphur from sulphur dioxide (SO2) containing gases. Key advantages are
reduced byproduct H2 and CO, reduced fuel consumption, no need for expensive catalyst, and reasonable operating and capital costs, and no soot formation on the catalyst bed with the sulphur recovery above 97% and overall recovery of 100%.
Thermal Reduction of Sulphur Dioxide to Sulphur in a Single ReactionFurnace
RATE CAPABILITIES, & QUALIFICATIONS – MINING and METALS
- Gas Cleaning Processes
- SO2 Concentration Using Physical or Chemical Solvents
- SO2 Liquefaction and Storage
- SO2 Reduction to Sulphur Technologies – New Patented Processes by RATE
(High Temperature Catalytic, and Low Temperature Catalytic technologies) - Zero Emission – 100% Overall Sulphur Recovery – by Recycling SO2 stream
from SO2 concentration unit to sulphur Recovery Unit - 100% Oxygen Enrichment
- Forced Draft Incineration with Heat Recovery System
- Sulphur Degassing and Granulation / Forming
- CO2 Capture
- Proprietary Furnace design
- Proprietary Burner Design
- Furnace Supply
- Burner Supply
- Catalyst supply
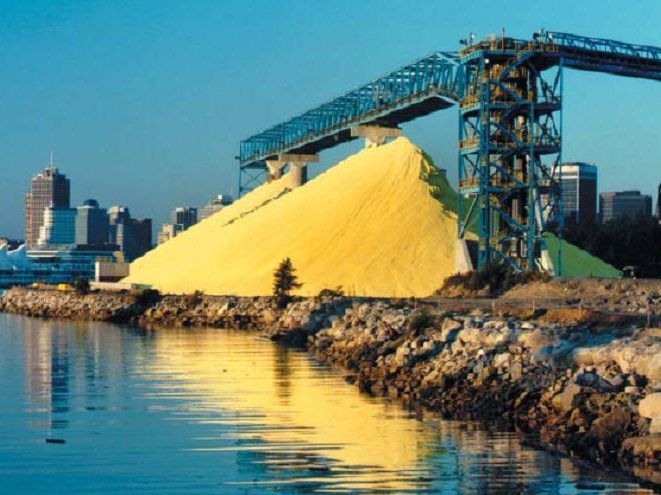